What are Bag In Bag Out (BIBO) Systems?
Bag In Bag Out (BIBO) Systems are specialized containment units designed to facilitate the safe removal and replacement of air filters in environments where hazardous particulates, pathogens, or toxic chemicals are present. The core principle of BIBO technology is to create a sealed, double-bagged barrier between the contaminated filter and the external environment during changeout procedures. This prevents the escape of hazardous materials and protects both personnel and facility infrastructure.
BIBO systems are engineered for use in applications with stringent contamination control requirements, including:
Pharmaceutical manufacturing cleanrooms
Biosafety laboratories (BSL-3 and BSL-4)
Healthcare isolation rooms and hospital HVAC systems
Chemical processing plants
Semiconductor fabrication facilities
A typical BIBO unit consists of a containment housing, a flexible changeout bag system, and secure access doors or ports. During filter replacement, operators use glove ports or sleeves to manipulate the filter from outside the containment area, ensuring that no direct contact occurs with hazardous materials. The contaminated filter is sealed within the inner bag, which is then detached and secured for safe disposal, while a new filter is installed using the outer bag.
For organizations seeking a trusted provider, YOUTH offers a comprehensive portfolio of BIBO solutions tailored to diverse industry needs.
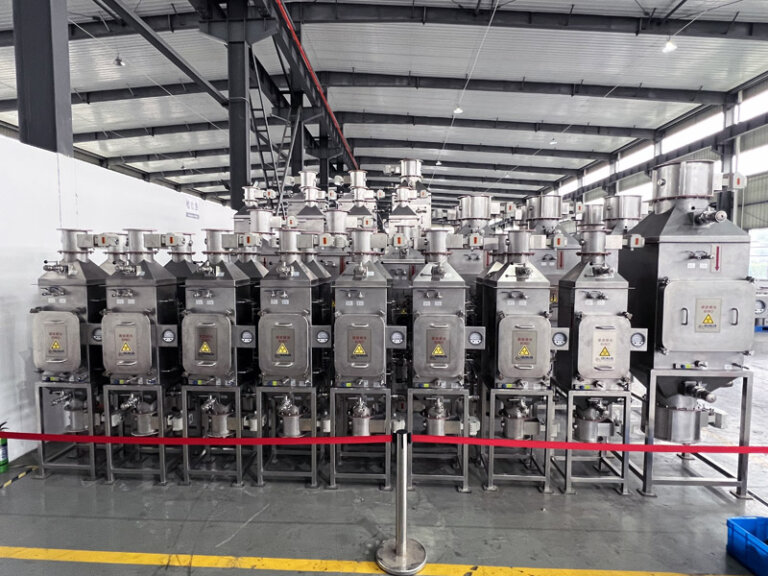
Different Types of Installation
- Fixed Installation Orientation: Choose between vertical or horizontal configurations during production.
- Tailored Selection: Pre-determine the installation type based on the required airflow capacity.
- Outdoor Adaptability: Equipped with an optional rain cover for outdoor setups.
Key Technical Specifications
Selecting the right Bag In Bag Out (BIBO) System requires a thorough understanding of its technical parameters and compliance with relevant industry standards. The following specifications are critical for B2B buyers evaluating BIBO solutions:
Specification | Description | Typical Values/Options |
---|---|---|
Filter Type | HEPA (99.97% @ 0.3μm), ULPA (99.9995% @ 0.12μm) | HEPA, ULPA |
Containment Level | Suitability for biosafety levels | BSL-2, BSL-3, BSL-4 |
Housing Material | Construction for chemical resistance and durability | 304/316L stainless steel, powder-coated steel |
Airflow Capacity | Maximum volumetric flow rate supported | 500–10,000 CFM |
Access Mechanism | Filter changeout interface | Glove ports, bag sleeves, pass-through doors |
Compliance Standards | Regulatory and industry certifications | EN 1822, ISO 14644, ASME AG-1, NSF 49 |
Monitoring & Alarms | Integrated differential pressure, leak detection, and filter life monitoring | Digital sensors, remote monitoring |
Modular Design | Expandability and integration with HVAC or process systems | Modular, customizable configurations |
Filter Efficiency and Containment: BIBO systems are typically equipped with HEPA or ULPA filters, capable of capturing particles as small as 0.12 microns with efficiencies up to 99.9995%. This ensures compliance with ISO 14644 cleanroom standards and CDC guidelines for infectious disease containment.
Construction Materials: The housing is commonly fabricated from 304 or 316L stainless steel for maximum corrosion resistance and ease of decontamination. Powder-coated steel options are available for less aggressive environments.
Airflow and Sizing: Systems are available in a range of airflow capacities, from compact units for laboratory fume hoods to large-scale modules for industrial HVAC integration. Sizing is determined by facility air change requirements and filter loading rates.
Access and Changeout Mechanisms: Advanced BIBO systems feature ergonomic glove ports, clear viewing panels, and integrated lighting to facilitate safe, efficient filter changeouts. Some models offer hands-free bagging and automated sealing to further reduce operator exposure.
Compliance and Validation: Leading BIBO solutions are designed to meet or exceed EN 1822 (filter performance), ISO 14644 (cleanroom classification), and ASME AG-1 (nuclear air and gas treatment) standards. Integrated monitoring systems provide real-time data on filter integrity, pressure differentials, and system status.
Standard Types of Bag in Bag out
Airflow (m³/h) | Efficiency Specs (mm) | Cabinet Size WHD (mm) |
250 | 305*305*95=1Chamber | 2100*455*375 |
700 | 305*305*292=1Chamber | 2100*455*375 |
1350 | 305*610*292=1Chamber | 2300*755*375 |
2700 | 610*610*292=1Chamber | 2300*755*680 |
5400 | 610*610*292=2Chamber | 2900*1560*680 |
8100 | 610*610*292=3Chamber | 2900*2365*680 |
10800 | 610*610*292=4Chamber | 2900*1560*1330 |
16200 | 610*610*292=6Chamber | 2900*2365*1330 |
Note: Adequate space must be allotted on-site for the “Bag in bag out” system to accommodate operations, installation of differential pressure gauges and piping, as well as for maintenance activities like filter replacement. The system allows for consecutive and stackable configuration for seamless integration and use.
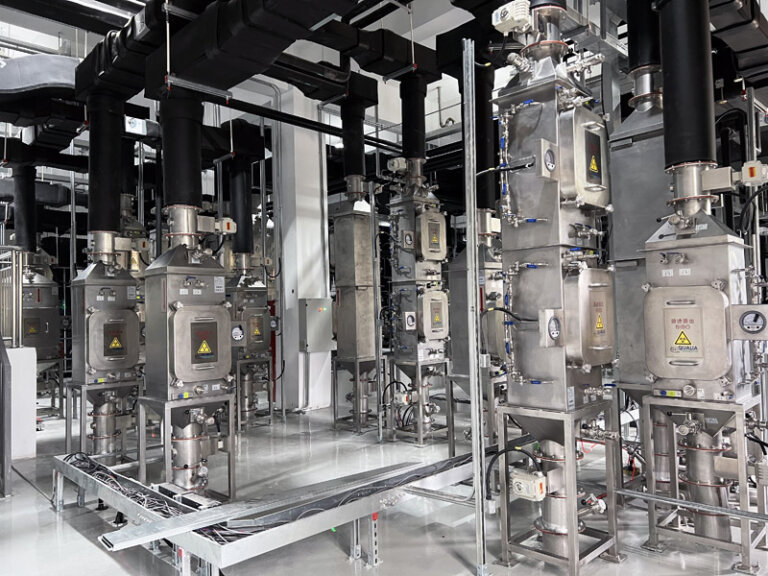
Product Features
- Construction: Entirely built with 3.0 mm 304 stainless steel full welds and surface vibration grinding. Connection flanges made from 5.0 mm 304 stainless steel.
- Filter Box Design: Conforms to the standard 292mm thickness high-efficiency gel seal filters, utilizing industry-leading non-partitioned super-fold stainless steel framed filters with lifespans more than double that of conventional partitioned or V-type filters.
- Internal Compression Mechanism: CNC machined from 304 stainless steel, ensuring resistance to oxidation and corrosion.
- Sealing Strip: Utilizes an EPDM medium density sealing strip for robust sealing capability.
- Scanning Mechanism: Made of 304 stainless steel with a linear scanning approach.
- Differential Pressure Gauges Pipeline: Includes needle-type filters to prevent leak risks during maintenance.
- Internal Setup: Stainless steel dust emission pipelines and outlets with diffusers to ensure upstream concentration uniformity.
- PAO test: Comes with upstream and downstream testing ports, both fitted with manual safety ball valves, and includes PAO supply and sampling port.
- VHP Disinfection Interface: Positioned on both the input and output sides, with downstream disinfection verification ports.
- Operation Modes: Manual and automatic scanning mode interfaces, with reserved scanning position signal ports.
- Protective Bags: Each door equipped with a protective bag approximately 2 meters in length, complete with full harness and safety strap.
- Filtration Options: Single high-efficiency filter unit available; multiple filtration stages can be added such as pre and medium-efficiency filters, chemical filters, activated carbon filters, or double high-efficiency filters for serial installation.
- Optional accessories: Sealed Valve for disinfection and air tightness tests, DOP scanning for filter efficiency, differential pressure gauge/sensor to monitor filter pressure changes, instrument protection system, disinfection ports, transition adapters for various diameters.
Product Certifications
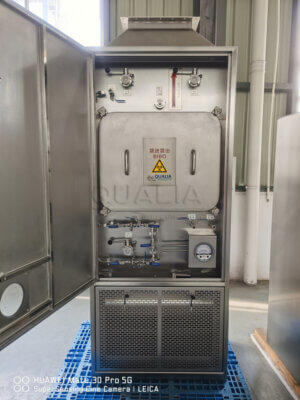
- Building Engineering Quality Supervision and Testing Center: Certification acquired.
- Patent Certificate: Patent accreditation granted.
- BETC Test Report: Comprehensive test report issued by BETC.
Business Benefits and ROI
Bag In Bag Out (BIBO) Systems deliver measurable business value across multiple dimensions, making them a strategic investment for organizations prioritizing safety, compliance, and operational efficiency.
1. Enhanced Personnel Safety
Eliminates direct contact with hazardous particulates during filter changeout, reducing risk of occupational exposure and associated health claims.
Minimizes potential for accidental releases, protecting both staff and facility assets.
2. Regulatory Compliance
Facilitates adherence to OSHA, CDC, and EPA requirements for hazardous material containment and air quality.
Streamlines audit processes with built-in monitoring, documentation, and validation features.
3. Reduced Downtime and Operational Disruption
Enables rapid filter changeouts—often 50% faster than traditional methods—minimizing process interruptions and production losses.
Modular design allows for maintenance without shutting down entire HVAC or process systems.
4. Lower Liability and Insurance Costs
Demonstrates proactive risk management, often resulting in lower insurance premiums and reduced legal exposure.
Provides documented containment procedures to support regulatory investigations and incident response.
5. Improved Total Cost of Ownership (TCO)
Durable construction and advanced monitoring reduce the frequency of unplanned maintenance and filter failures.
Extended filter life and optimized changeout scheduling lower consumables costs over time.
Business Outcome | Traditional Filter Housing | Bag In Bag Out (BIBO) Systems |
---|---|---|
Filter Changeout Time | 2–3 hours | 45–60 minutes |
Personnel Exposure Risk | High | Minimal |
Regulatory Audit Readiness | Manual records | Automated, validated |
Annual Maintenance Cost | High | Moderate |
Insurance Premium Impact | Neutral | Favorable |
Industry Use Cases:
In the manufacturing sector, BIBO systems have enabled continuous production in cleanrooms by allowing filter changes without full system shutdown.
Healthcare organizations implementing BIBO technology in isolation rooms have reported a 60% reduction in staff exposure incidents.
Financial services clients with data center cleanrooms have leveraged BIBO systems to maintain uptime and ensure compliance with air quality standards for sensitive electronics.
Implementation Scenarios and Industry Use Cases
Bag In Bag Out (BIBO) Systems are deployed across a diverse range of industries, each with unique containment challenges and regulatory requirements.
Pharmaceutical Manufacturing
BIBO systems are integral to GMP-compliant cleanrooms, ensuring that cross-contamination between production batches is eliminated.
Automated monitoring and documentation features support FDA audits and validation processes.
Biotechnology and Biosafety Laboratories
High-containment BSL-3 and BSL-4 labs rely on BIBO systems to safely manage pathogens and genetically modified organisms (GMOs).
Modular BIBO units allow for rapid reconfiguration as research priorities evolve.
Healthcare and Hospitals
Used in isolation rooms and infectious disease wards to prevent the spread of airborne pathogens such as tuberculosis and COVID-19.
Enables maintenance staff to replace filters without entering contaminated zones, reducing infection risk.
Chemical Processing and Semiconductor Manufacturing
Protects personnel from toxic chemical vapors and particulates generated during manufacturing processes.
Ensures compliance with ISO 14644 and SEMI S2 standards for cleanroom environments.
Industry Sector | Typical Application | Key Benefits | Compliance Focus |
---|---|---|---|
Pharmaceuticals | Cleanroom HVAC | Contamination control, GMP | FDA, EU GMP |
Biotechnology | BSL-3/4 Lab Ventilation | Pathogen containment | CDC, NIH, WHO |
Healthcare | Isolation Room Filtration | Infection control, safety | OSHA, CDC |
Semiconductors | Cleanroom Air Handling | Particle control, uptime | ISO 14644, SEMI S2 |
Chemical Processing | Process Exhaust | Operator safety, emissions | EPA, OSHA |
Implementation Considerations:
Integration with existing building management and HVAC systems is typically straightforward, but older facilities may require custom retrofitting.
Training for maintenance staff is essential to ensure proper bagging and sealing procedures.
Remote monitoring and digital documentation streamline compliance reporting and preventive maintenance.
Application
- Pharmaceutical Engineering: Exhaust systems for vaccine production areas, air supply and exhaust for vaccine laboratory animal rooms, as well as for spaces producing hormone-class and cytotoxic medicines, high-activity chemical production, and anticancer preparation manufacturing.
- Bio-safety Laboratories: Supply and exhaust air management.
- Hospital Isolation Zones: Exhaust air systems.
- Industrial Chemical Emissions: Handling the discharge of chemical gases.
- Nuclear Power Plants and Fuel Processing Facilities: Dealing with air exhaust and filtration.
- Animal Disease Laboratories: Managing air supply and exhaust.
- Toxic Waste Isolation Facilities: Air management for isolated environments.
- Industrial, Research, and Military Facilities: Managing air supply and exhaust for areas dealing with chemicals, biological agents, radiological and carcinogenic materials.
- Biomedical Research and Genetic Engineering Facilities: Air supply and exhaust systems management.
- Pharmaceutical Laboratories: Providing secure exhaust air systems.
Bag in Bag out Gallery
Competitive Landscape and Differentiation
When evaluating Bag In Bag Out (BIBO) Systems, it is essential to compare them against alternative containment solutions and identify key differentiators that impact long-term value.
Feature/Attribute | BIBO Systems | Traditional Filter Housings | Bubble/Negative Air Tents |
---|---|---|---|
Personnel Exposure Risk | Minimal (sealed changeout) | High (direct contact) | Moderate |
Filter Changeout Time | 45–60 minutes | 2–3 hours | 1–2 hours |
Modular Design | Yes | Limited | No |
Compliance Documentation | Automated | Manual | Manual |
Integration Flexibility | High | Moderate | Low |
Upfront Cost | Higher | Lower | Moderate |
Long-Term TCO | Lower (fewer incidents) | Higher (more failures) | Moderate |
Advanced Monitoring | Standard | Rare | Rare |
Key Differentiators:
Hands-Free Changeout: BIBO systems eliminate direct filter handling, reducing exposure and contamination risk.
Modular, Scalable Design: Easily integrates with new or existing HVAC/process systems and allows for future expansion.
Advanced Monitoring: Real-time digital sensors and remote diagnostics support predictive maintenance and compliance.
Regulatory Alignment: Designed to meet or exceed global standards for biosafety and cleanroom operation.
Market Positioning:
BIBO systems are best suited for organizations with high-stakes contamination risks, strict regulatory oversight, and a need for validated, auditable processes.
While traditional housings may offer lower upfront costs, the long-term risk profile and operational inefficiencies make BIBO systems the preferred choice for mission-critical applications.
Procurement Considerations
For procurement teams evaluating Bag In Bag Out (BIBO) Systems, several key factors should guide the decision-making process:
Total Cost of Ownership (TCO)
Consider not only the initial capital investment but also long-term savings from reduced downtime, fewer contamination incidents, and lower insurance premiums.
Evaluate filter life, maintenance intervals, and consumables costs.
Implementation Timeline and Requirements
Assess the lead time for system delivery, installation, and commissioning.
Identify any facility modifications or retrofits required for integration.
Integration with Existing Systems
Ensure compatibility with current HVAC, building management, and monitoring platforms.
Review available interfaces for digital monitoring and remote diagnostics.
Training and Support
Confirm availability of comprehensive training for maintenance and operations staff.
Evaluate the vendor’s support infrastructure, including response times, spare parts availability, and remote troubleshooting.
Scalability and Future-Proofing
Select systems with modular architecture to accommodate future facility expansions or changing regulatory requirements.
Prioritize solutions with upgradable monitoring and control features.
Procurement Factor | Recommended Evaluation Criteria |
---|---|
TCO | 5-year cost projection, incident history |
Implementation Timeline | 8–12 weeks typical, site-specific factors |
Integration | Open protocols (BACnet, Modbus), APIs |
Training | Onsite, virtual, and documentation |
Support | 24/7 hotline, local service partners |
Scalability | Modular units, expansion kits |
Vendor Checklist:
Proven track record in regulated industries
Documented compliance with EN 1822, ISO 14644, ASME AG-1
References from similar implementation scenarios
Flexible service level agreements (SLAs)
Limitations and Challenges
While Bag In Bag Out (BIBO) Systems offer substantial advantages, it is important to acknowledge their limitations to ensure informed decision-making:
Higher Upfront Investment: BIBO systems require a greater initial capital outlay compared to traditional filter housings, though this is often offset by long-term savings.
Maintenance Complexity: Proper bagging and sealing procedures necessitate specialized training for maintenance personnel. Inadequate training can compromise containment integrity.
Integration with Legacy Infrastructure: Retrofitting older facilities can be challenging, particularly where space constraints or outdated HVAC systems are present. Custom engineering may be required.
Organizations should weigh these factors against the potential risks and costs of alternative containment methods, considering both immediate and long-term business impacts.
Conclusion and Next Steps
Bag In Bag Out (BIBO) Systems set the benchmark for safe, efficient, and compliant filter containment in high-risk environments. By combining advanced engineering, modular design, and automated monitoring, BIBO systems deliver unmatched protection for personnel, assets, and business continuity. For organizations seeking to elevate their contamination control strategy and future-proof their operations, partnering with an experienced provider is essential.
To explore tailored BIBO solutions for your facility, consult with a trusted industry leader and request a detailed assessment of your containment requirements.
Related Contents:
- Safe Hazardous Material Handling with BIBO
- Bag-in Bag-out System Market Trends 2025 – Biosafety Integration Data
- Bag-In-Bag-Out Housing Applications in Pharmaceutical Manufacturing
- Emerging Trends: The Future of BIBO Technology
- Ensuring Compliance: BIBO and Industry Standards
- Essential BIBO System Maintenance Checklist
- Bag-In-Bag-Out Containment for Biopharmaceutical Processing – 27 CFR Compliance
- Stainless Steel Air Showers: Durable Cleanliness
- Bag-In-Bag-Out Housing Systems – ISO 14644 Compliant Filtration Specifications