What is the Air Shower?
QUALIA’s air shower is a specialized enclosed chamber used in cleanroom environments to remove surface particles from individuals and objects before they enter a controlled environment. The purpose of the air shower is to minimize the introduction of dust, fibers, and other contaminants that can adhere to clothing or equipment, which can otherwise compromise the sterility and cleanliness of a cleanroom or laboratory space.
Air showers are essential in various industries like pharmaceutical manufacturing, biotechnology, electronics production, and other scientific fields that require stringent contamination control. They effectively serve as an intermediate purification step between the outside environment and the cleanroom to help maintain the integrity of the cleanroom’s controlled environment.
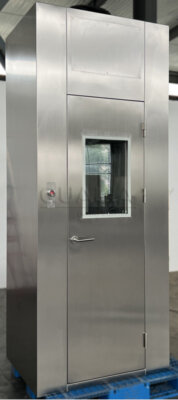
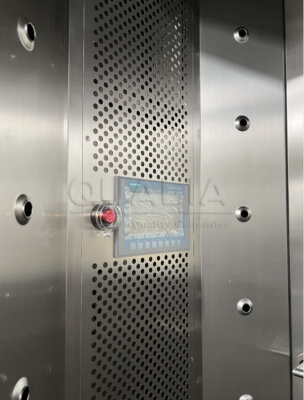
Superior Material and Safety Design
- The entire casing is made of 1.5mm thick high-quality stainless steel, surpassing industry durability standards. Stainless steel prevents paint peeling, and the 1.5mm thickness ensures long-term stability and deformation resistance.
- Uses stainless steel frames and doors with double-layered 5mm glass for transparency while minimizing safety risks associated with large glass surfaces. The double-layered glass structure protects the door from breaking, even in the event of accidental collisions during transport.
- The concealed closing arm provides a cleaner, more modern appearance, with mechanical parts cleverly hidden within the door’s interior structure.
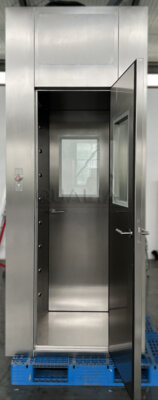
Innovative Nozzle and Air Shower Room
- Our innovative integrated stainless steel nozzle significantly reduces hygiene blind spots compared to traditional nozzles. This unified design ensures the integrity of the nozzle inside and out, preventing contaminants from accumulating at the seams, thereby greatly reducing cleaning difficulty.
- Our air shower rooms are equipped with 32 to 40 integrated stainless steel nozzles, distributed evenly on all four sides, depending on the specific height of the air shower room. This increased number of nozzles, along with a larger coverage area, ensures comprehensive and uniform airflow from top to bottom. The specially designed top and bottom nozzles, located approximately 100mm from the ceiling and floor, achieve near-perfect uniformity in cleaning effectiveness.
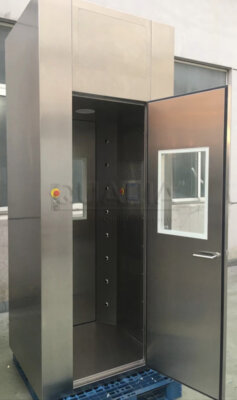

Efficiency and Comfort
- The innovative return air grille design, set parallel to the nozzles, can immediately remove dust particles from the air during the dust removal process, significantly improving the efficiency of the air shower room. With this unique feature, our air shower room’s dust removal performance far exceeds standard products on the market.
- Equipped with sealing gaskets to effectively prevent dust and reduce external noise to below 65 decibels, providing a good working environment.
Ease of Cleaning and Control
- Except for control buttons, all mounted panels are flush with the main body of the machine, making cleaning easier and eliminating frustrating hygiene dead angles.
- Under microcontroller control, single-level password adjustment parameters can be set. Under Siemens PLC control, 3-4 levels of authority can be designed for tiered management. Emergency stop buttons can also be locked. All these features prevent operator errors.
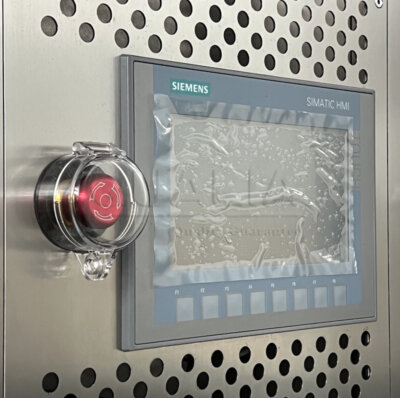
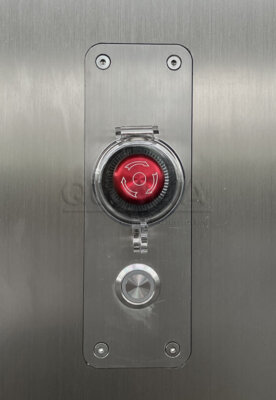
Maintenance Design
- Fans and filtering systems employ a unique independent configuration, unlike traditional models on the market that often require disassembly of the filtering device for any fan maintenance, leading to increased downtime and a more cumbersome maintenance process.
- Our design allows for simultaneous maintenance of fans and filters. The replacement of filters can be done without interrupting fan operation, and fan replacement only requires removing the top panel of the device. Thanks to the rotatory design, the replacement process significantly simplifies the steps needed for regular maintenance.
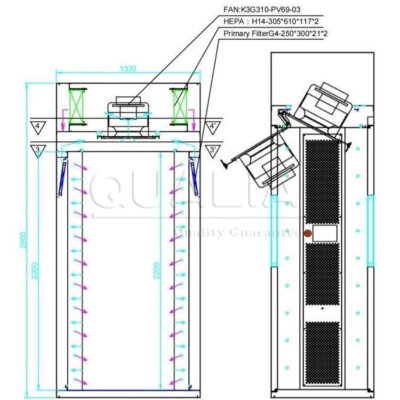
Related Contents:
- Double-Chamber VHP Passbox: Enhancing Efficiency and Flexibility
- Ensuring Safety with Bag-in/Bag-out: The Definitive Guide to Hazardous Filter Replacement
- Navigating Biocontainment: The Critical Differences Between BSL-3 and BSL-4 Labs
- Introducing Qualia: Advanced OEB5 Grade Protection with Bag-In Bag-Out (BIBO) System
- Introducing Our Custom-Designed Dry Isolation Weighing Chamber for European Clients
- What is the HS Code for “Bag in Bag Out”?
- What is the process of bag in bag out?
- Understanding the Differences Between Stationary and Mobile BSL-3/BSL-4 Laboratories
- Join Qualia at ACHEMA 2024 in Frankfurt, Germany