Modern pharmaceutical and biotechnology facilities face unprecedented challenges in managing liquid waste streams that contain active pharmaceutical ingredients (APIs), biological agents, and complex chemical compounds. Regulatory bodies worldwide are implementing stricter discharge limits, while facilities must balance operational efficiency with environmental compliance. An Effluent Decontamination System provides the advanced treatment capabilities necessary to address these evolving requirements, ensuring safe discharge while protecting both public health and environmental resources.
How to Ensure Standard Sterilization Time F0=30?
By controlling the temperature and time of heating:
- Continuous heating at 121°C for 30 minutes
- Continuous heating at 130°C for 3.9 minutes
- Continuous heating at 135°C for 75 seconds
- Continuous heating at 140°C for 24 seconds
- Continuous heating at 145°C for 8 seconds
Note: Using thermophilic Bacillus stearothermophilus as the microbial indicator.
Equipment Selection:
Daily processing capacity: 100L/200L/300L (other capacities can be customized).
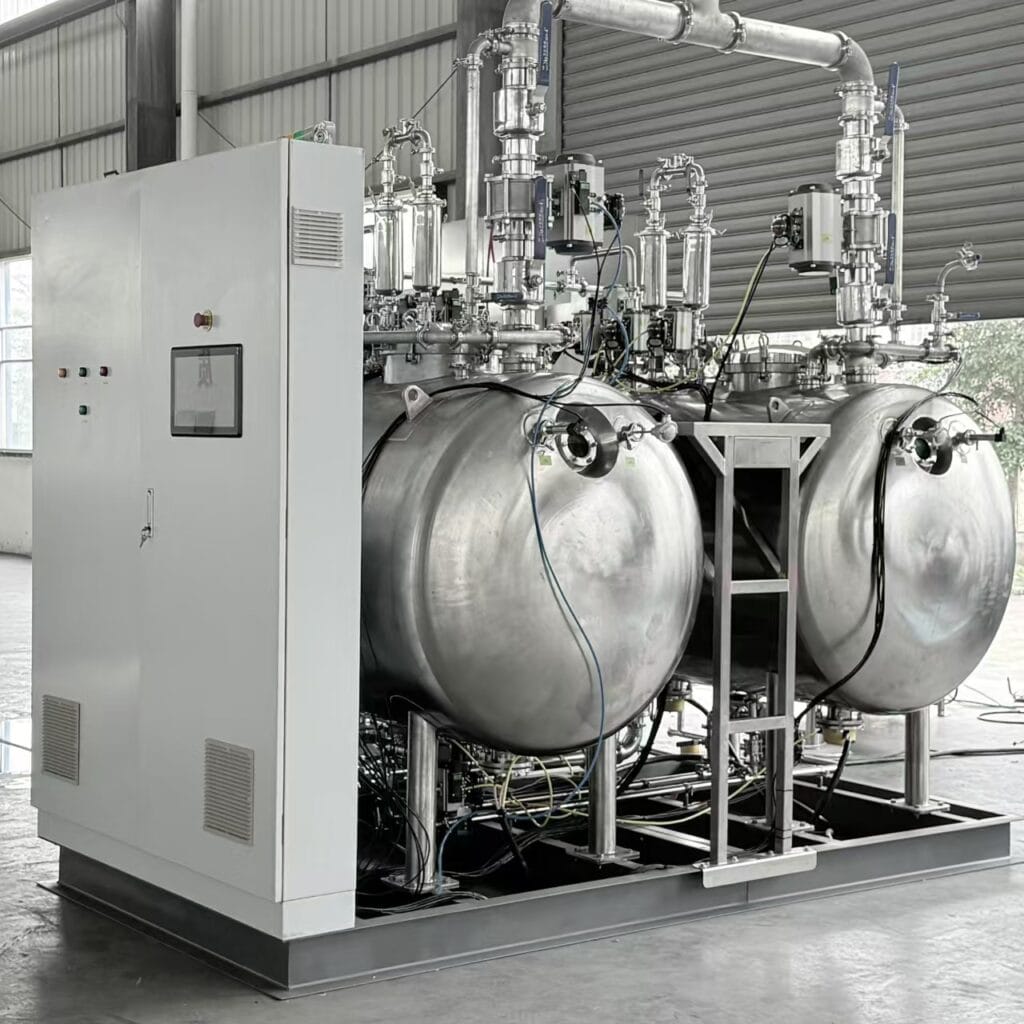
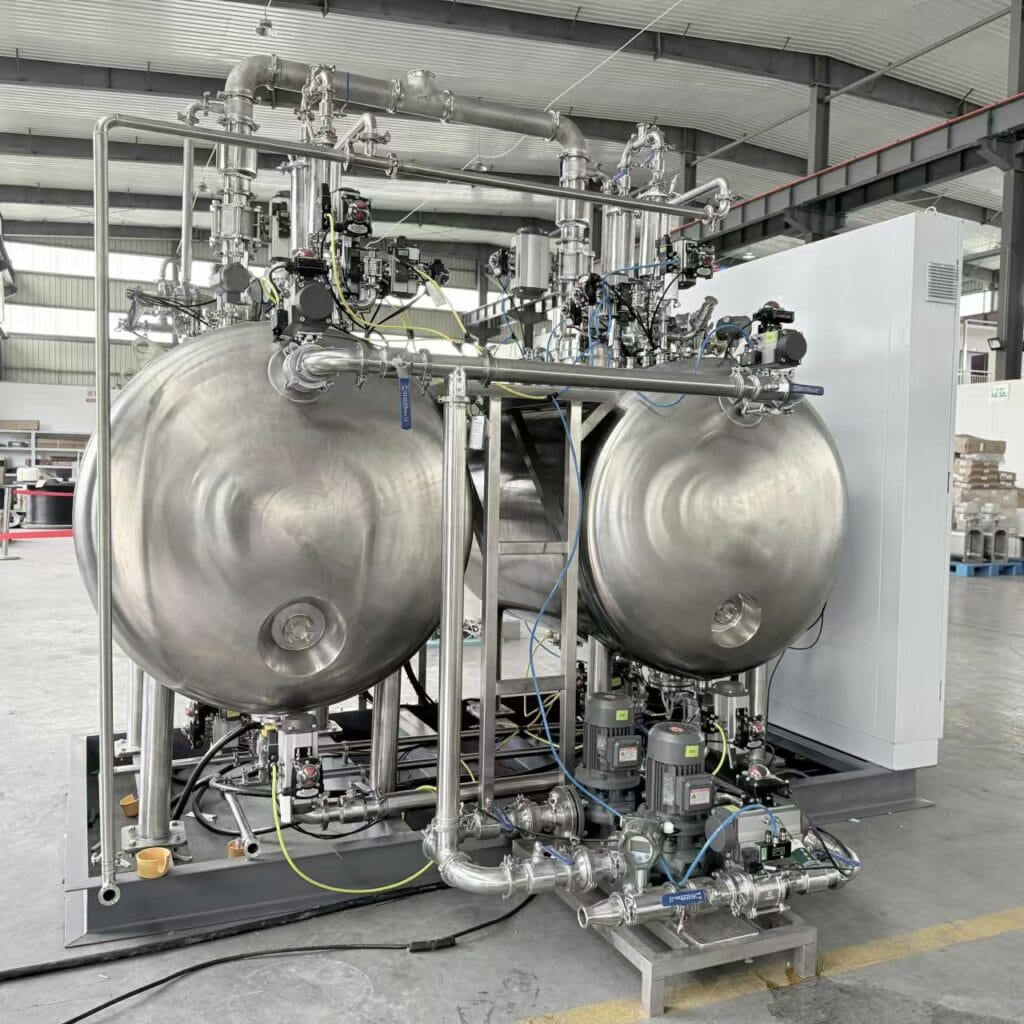
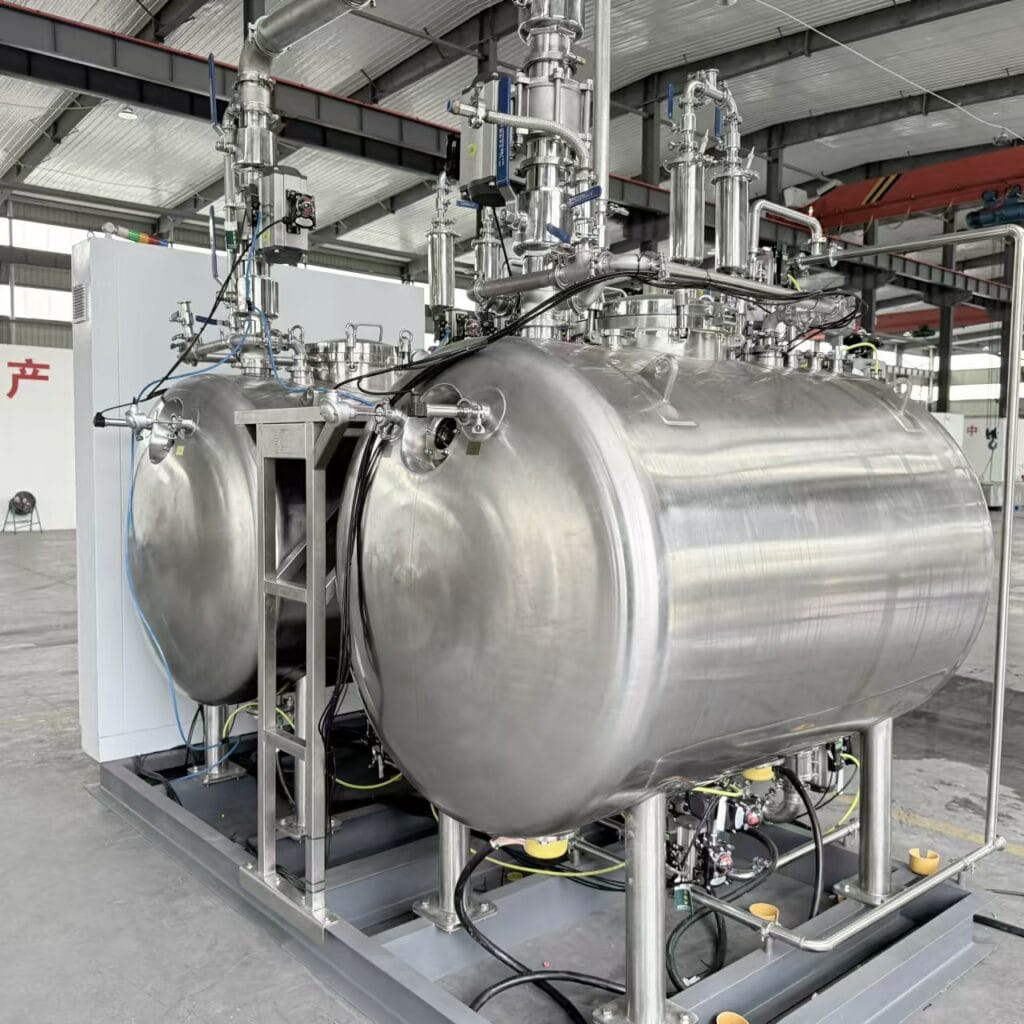
Understanding Effluent Decontamination System Technology
An effluent decontamination system for pharmaceutical facilities represents a sophisticated approach to treating liquid waste streams that conventional municipal treatment cannot adequately handle. These systems employ multiple treatment barriers including thermal inactivation, chemical oxidation, and advanced filtration to achieve validated sterilization levels.
The core functionality centers on continuous flow decontamination using precise temperature and pressure control. Modern systems typically operate at temperatures between 130°C and 165°C with exposure times ranging from 3 seconds to several minutes, depending on the specific contamination risk level. This thermal approach achieves validated F0 values—a pharmaceutical industry standard measuring sterilization efficacy—with F0 values of 15 or higher commonly achieved through 1.16 seconds at 150°C.
Chemical treatment integration supplements thermal processes through targeted oxidation. Advanced systems utilize hydrogen peroxide, peracetic acid, or ozone-based processes to break down recalcitrant pharmaceutical compounds that resist conventional treatment. Research demonstrates that combined ozone and hydrogen peroxide processes can achieve 75-88.5% chemical oxygen demand (COD) reduction across varying pH levels.
Membrane filtration technologies provide a final barrier, removing particulates and ensuring consistent effluent quality. Systems incorporate pre-filtration for solids larger than 1.2mm, followed by ultrafiltration or reverse osmosis depending on discharge requirements. This multi-barrier approach enables facilities to handle diverse waste streams from cell culture operations, fermentation processes, and analytical laboratories.
The adaptability of modern systems allows for BSL-2 BSL-3 BSL-4 effluent treatment with validated performance across different containment levels. Each biosafety level requires specific decontamination protocols, with BSL-3 and BSL-4 facilities mandated by law to implement validated effluent treatment.
▶ Request Technical Documentation ◀
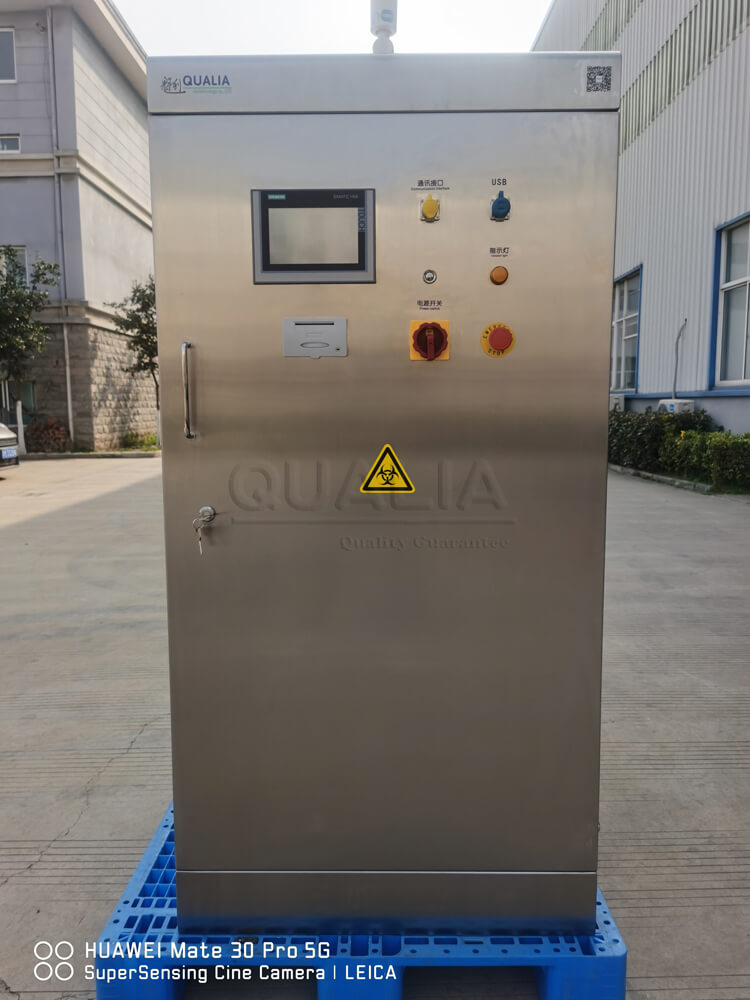
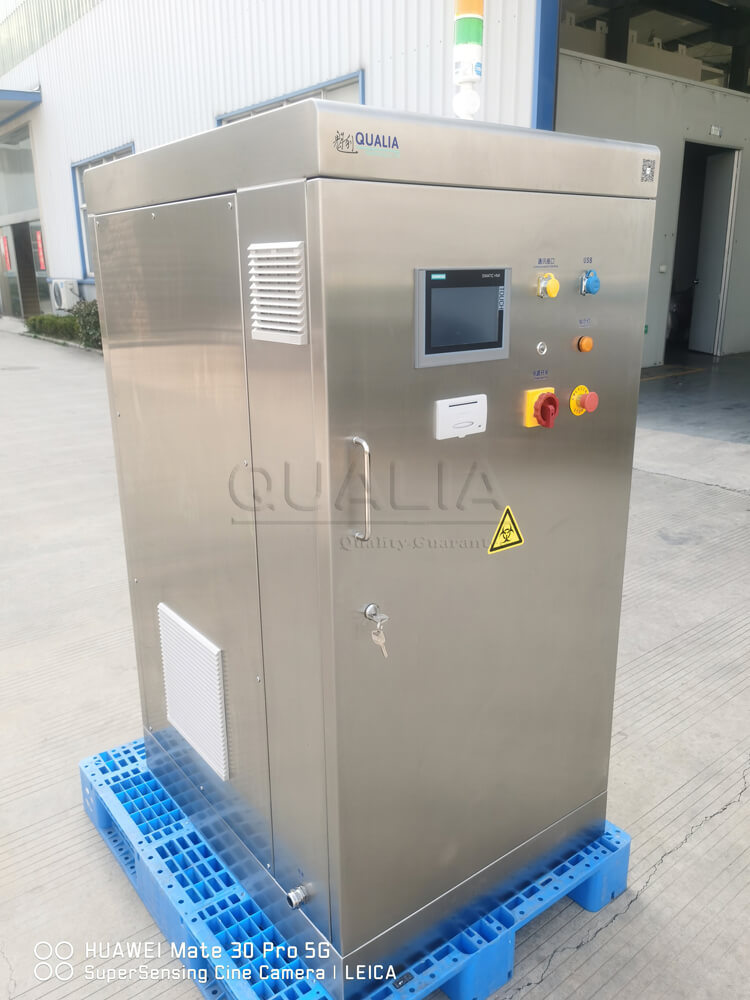
Technical Specifications and Performance Standards
System Parameter | Continuous Flow Systems | Batch Systems | Chemical Treatment |
---|---|---|---|
Operating Temperature | 130-165°C | 121-134°C | Ambient-60°C |
Exposure Time | 3-600 seconds | 15-60 minutes | 30 minutes-2 hours |
Sterilization Efficacy | F0 15-50 | F0 15-100 | 6-log reduction |
Capacity Range | 500-350,000 L/day | 70-10,000 L/batch | Variable |
Energy Recovery | 80% thermal recovery | Limited | N/A |
Performance benchmarks for effluent decontamination systems demonstrate consistent results across different facility types. A pharmaceutical treatment plant in Switzerland achieved over 90% reduction in pollutant levels using advanced oxidation processes. Similarly, facilities in India and the United States have reported removal rates approaching 100% for many pharmaceutical compounds through integrated biological and membrane treatment approaches.
Validation requirements follow established pharmaceutical industry standards with biological indicators confirming >10^6 spore reduction. Continuous monitoring systems track critical parameters including temperature, pressure, flow rate, and residence time to ensure consistent performance. Annual verification protocols include system component testing, biological validation, and HEPA filter certification where applicable.
Compliance Standard | Requirement | System Response |
---|---|---|
FDA 21 CFR 211 | Validated sterilization | Continuous monitoring, documented cycles |
ISO 17665 | Steam sterilization | Temperature/time validation |
EPA Discharge Limits | Pollutant reduction | Multi-barrier treatment |
BSL Containment | Biological inactivation | Thermal + chemical backup |
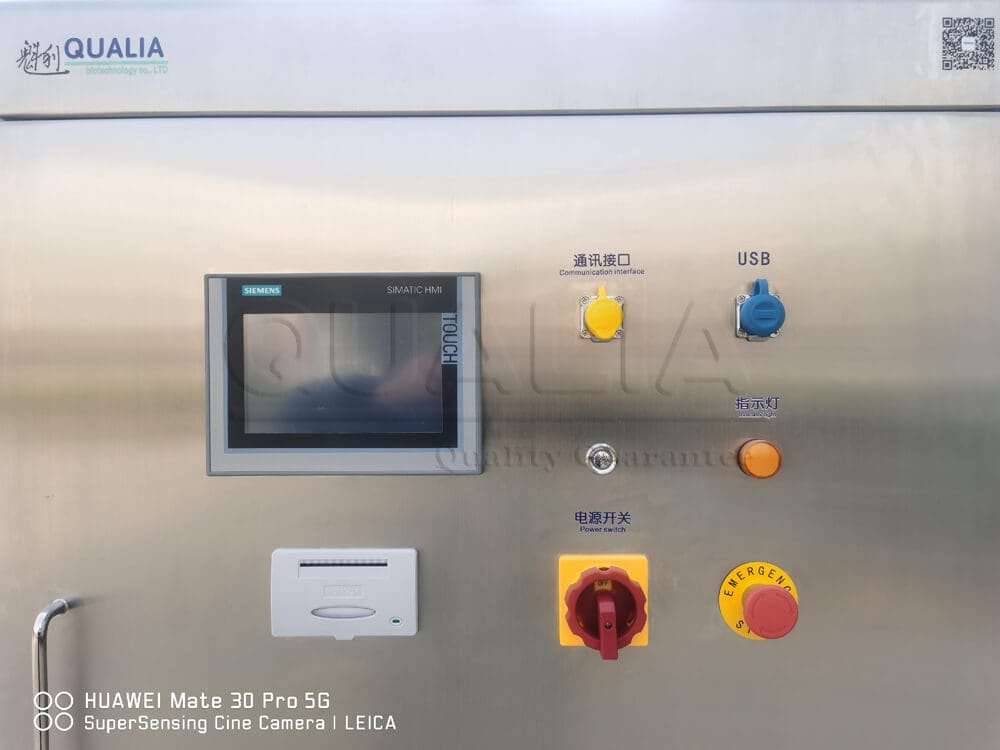
Real-World Applications and Customer Experiences
Pharmaceutical Manufacturing Implementation:
A Southeast European biotech company recently commissioned an advanced biopharma wastewater decontamination system capable of processing 46 cubic meters per hour. The system combines biological processes, dissolved air flotation, and chemical-physical treatment to remove all traces of APIs from wastewater. Implementation included digital monitoring through WaterExpert™ platform, providing real-time data analysis and troubleshooting support.
The integration of multiple treatment technologies has enabled us to consistently meet discharge requirements while reducing operational complexity. —EnviroChemie Case Study
Research Facility Applications:
High-containment research facilities utilizing automated effluent sterilization systems report significant improvements in operational efficiency. A facility processing BSL-3 materials implemented a continuous flow system with 1,000 L/hour capacity, achieving validated sterilization while reducing energy consumption through integrated heat recovery. The system’s automatic CIP (Clean-in-Place) cycles reduced maintenance requirements by approximately 40%.
Biotech Manufacturing Scale-Up:
Manufacturing facilities transitioning from pilot to commercial scale benefit from modular system designs. One implementation scaled from 2,500 L/day to 100,000 L/day capacity using continuous flow technology, maintaining consistent F0 values throughout the expansion. The modular approach enabled phased implementation without disrupting existing operations.
Facility Type | Typical Capacity | Primary Treatment | Validation Level |
---|---|---|---|
Research Labs | 70-5,000 L/day | Thermal batch | F0 15-30 |
Pilot Manufacturing | 2,500-25,000 L/day | Continuous thermal | F0 30-50 |
Commercial Production | 50,000-350,000 L/day | Multi-barrier | F0 50+ |
▶ Discuss Your Specific Requirements ◀
Implementation Approach and Support Framework
Phase 1: Assessment and Design (2-4 weeks)
Initial implementation begins with comprehensive effluent characterization and regulatory requirement analysis. Engineering teams evaluate existing infrastructure, utility availability, and integration points. Custom system configuration addresses specific waste stream characteristics including solids content, chemical composition, and required throughput capacity.
Phase 2: System Installation (4-8 weeks)
Installation typically requires coordination with facility operations to minimize disruption. Systems incorporate redundant monitoring equipment and automated controls to ensure reliable operation. Energy recovery systems, where applicable, integrate with existing steam or electrical infrastructure to optimize operational efficiency.
Phase 3: Validation and Training (2-3 weeks)
Comprehensive validation protocols include biological challenge testing, temperature distribution studies, and process monitoring verification. Operator training covers system operation, maintenance procedures, and troubleshooting protocols. Documentation packages ensure regulatory compliance and support ongoing quality assurance programs.
Implementation Phase | Duration | Key Activities | Deliverables |
---|---|---|---|
Assessment | 2-4 weeks | Site survey, requirements analysis | System specification |
Design | 3-6 weeks | Engineering, permit applications | Installation drawings |
Installation | 4-8 weeks | Equipment setup, integration | Operational system |
Validation | 2-3 weeks | Performance testing, training | Qualification documentation |
Ongoing Support Structure:
Post-installation support includes preventive maintenance programs, performance monitoring, and regulatory compliance assistance. QUALIA Bio-Tech provides comprehensive support packages including spare parts inventory, technical assistance, and system upgrades as regulations evolve.
▶ Schedule Implementation Consultation ◀
System Process Architecture
Collection and Segregation Framework
Initial Capture Protocol: Advanced collection systems automatically segregate effluent streams based on contamination risk assessment and source classification. Modern facilities utilize smart routing technology that directs waste streams to appropriate treatment pathways based on real-time analysis.
Risk-Based Segregation: Effluents undergo automated classification into high-risk (BSL-3/4 biological agents), medium-risk (pharmaceutical APIs), and low-risk (general laboratory waste) categories. This segregation optimizes treatment efficiency and reduces overall processing costs by 25-40%.
Pre-Treatment Optimization
Advanced Screening Systems: Multi-stage filtration removes particles ranging from 10mm down to 0.1mm using rotating drum screens and micro-strainers. This prevents downstream equipment damage and extends membrane life by up to 60%.
Dynamic pH Adjustment: Automated pH control systems maintain optimal conditions (typically 6.5-8.5) using real-time monitoring and precision chemical dosing. This optimization improves subsequent treatment efficacy by 15-30%.
Primary Treatment Technologies
Validated Thermal Processing: Continuous flow systems achieve sterilization temperatures of 130°C-165°C with precise residence time control (3-600 seconds). F0 sterilization values of 15-50 ensure >6-log pathogen reduction across all biological contaminants.
Multi-Chemical Disinfection: Sequential application of chlorine dioxide, ozone (0.5-2.0 mg/L), and hydrogen peroxide (10-50 mg/L) provides comprehensive pathogen neutralization. Advanced oxidation processes achieve 85-95% removal of recalcitrant pharmaceutical compounds.
High-Performance Filtration: Membrane bioreactors (MBR) with 0.04-0.4 micron pore sizes remove 99.9% of suspended solids and microorganisms. Activated carbon systems provide final polishing for trace organic removal.
Advanced Treatment Integration
Biological Treatment Optimization: Enhanced activated sludge processes with biomass concentrations of 8,000-12,000 mg/L achieve >90% BOD reduction. Anaerobic digestion systems provide energy recovery through biogas production (60-70% methane content).
Advanced Oxidation Processes (AOPs): UV/H2O2 systems operating at 254nm wavelength with hydrogen peroxide concentrations of 10-100 mg/L degrade complex pharmaceutical compounds with >95% efficiency. Ozone/UV combinations achieve mineralization of persistent organic pollutants.
Selective Ion Exchange: Specialized resins target heavy metals (lead, mercury, cadmium) achieving <0.01 mg/L discharge concentrations. Regeneration cycles extend resin life to 2-3 years with 95% recovery efficiency.
Monitoring and Quality Assurance Framework
Real-Time Process Control: Continuous monitoring systems track 15+ critical parameters including temperature (±0.1°C), pH (±0.05 units), turbidity, and biological activity. SCADA integration enables remote monitoring and automated response protocols.
Regulatory Compliance Verification: Automated sampling systems collect representative samples every 2-4 hours for laboratory analysis. Real-time sensors provide immediate alerts for parameter deviations exceeding ±5% of set points.
Controlled Discharge Protocols
Multi-Point Quality Verification: Final effluent undergoes automated testing for residual disinfectants, pH, temperature, and biological indicators before discharge authorization. Fail-safe systems prevent non-compliant discharge through automated valve closure.
Industry-Specific Applications
Biological Research Facilities
High-Containment Laboratories: BSL-3 and BSL-4 facilities require validated 6-log biological reduction with continuous monitoring and emergency containment protocols. Systems handle genetically modified organisms, select agents, and hazardous chemicals with zero discharge tolerance.
Medical and Healthcare Facilities
Hospital Effluent Management: Treatment systems process infectious waste from patient care areas, surgical suites, and pathology laboratories. Specialized protocols address antibiotic-resistant organisms and chemotherapy drug residues with >99.9% removal efficiency.
Pharmaceutical Manufacturing
API Waste Processing: Advanced systems handle active pharmaceutical ingredients, synthesis by-products, and cleaning solvents. Multi-barrier treatment achieves >95% API removal while recovering valuable materials through selective separation processes.
Agricultural Operations
Livestock and Processing Facilities: Large-scale systems process animal waste containing pathogens, nutrients, and veterinary drug residues. Biological treatment with nutrient recovery produces irrigation-quality water while generating biogas for energy production.
Technology Advancement Trends
Nanotechnology Integration
Nano-Enhanced Filtration: Graphene oxide membranes and carbon nanotube filters achieve molecular-level separation with 50% less energy consumption than conventional systems. Nano-catalysts enhance oxidation processes while reducing chemical consumption by 30-40%.
Artificial Intelligence Applications
Predictive Analytics: Machine learning algorithms analyze historical performance data to predict equipment failures 7-14 days in advance. AI-driven optimization reduces energy consumption by 15-25% while maintaining treatment efficacy.
Automated Process Control: Neural networks continuously optimize treatment parameters based on influent characteristics and discharge requirements. Real-time adjustments improve efficiency by 20-35% compared to manual operation.
Sustainable Chemistry Solutions
Green Disinfection Technologies: Electrochemical oxidation generates disinfectants on-site from salt water, eliminating chemical storage and transportation. Plasma-based systems achieve sterilization without chemical additives while reducing operational costs by 25-45%.
Bio-Based Treatment Agents: Enzymatic treatment systems use naturally occurring enzymes to break down specific pharmaceutical compounds. These systems achieve >90% removal efficiency while producing biodegradable by-products.
Frequently Asked Questions
Q: What capacity range do industrial effluent treatment solutions typically handle?
Modern effluent decontamination systems range from small laboratory applications processing 70 liters per day to large manufacturing facilities handling 350,000 liters daily. Continuous flow systems generally provide higher capacity efficiency compared to batch systems, with some installations processing over 90,000 gallons per day while maintaining compact footprints of less than 9 square meters.
Q: How do validation requirements differ between BSL containment levels?
BSL-2 facilities typically require validated 4-log microbial reduction, while BSL-3 and BSL-4 facilities mandate 6-log reduction with documented biological indicator testing. Higher containment levels also require additional monitoring systems, emergency procedures, and more frequent validation cycles to ensure continued compliance with containment protocols.
Q: What are typical operational costs for automated effluent sterilization systems?
Operating costs vary significantly based on system size, treatment requirements, and local utility rates. Energy consumption for thermal systems ranges from 15-30 kWh per cubic meter treated, with heat recovery systems reducing consumption by up to 80%. Chemical treatment costs depend on waste stream characteristics but typically range from $2-8 per cubic meter for pharmaceutical applications.
Q: How do these systems integrate with existing facility infrastructure?
Integration considerations include steam supply requirements (5-7 bar for continuous systems), electrical connections (typically 400V three-phase), and effluent collection systems. Most installations utilize gravity feed systems located in facility basements, though pump-fed configurations accommodate different architectural constraints. Control system integration enables remote monitoring and data logging for compliance documentation.
Q: What regulatory compliance documentation is provided?
Complete validation packages include Installation Qualification (IQ), Operational Qualification (OQ), and Performance Qualification (PQ) documentation. Systems provide continuous data logging for temperature, pressure, flow, and sterilization parameters. Annual recertification support ensures ongoing compliance with evolving regulatory requirements.
▶ Connect with Technical Team ◀
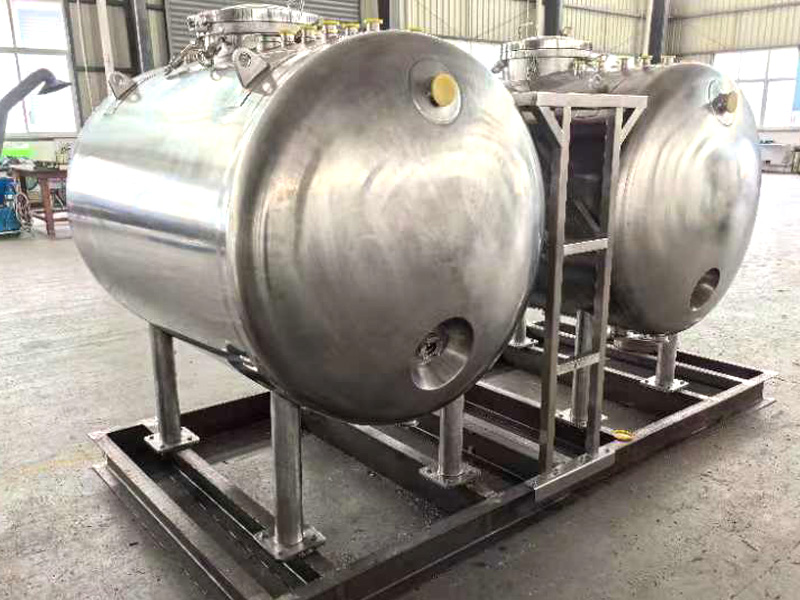
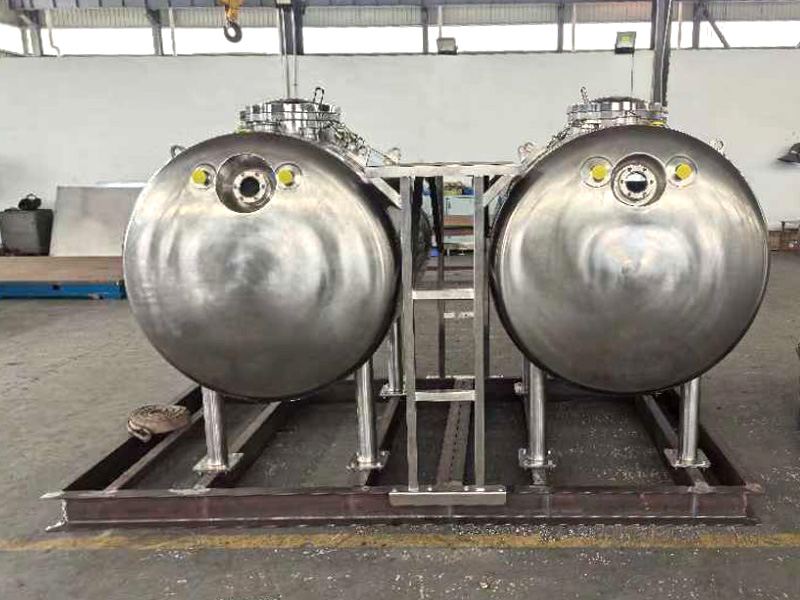
Market Position and Competitive Landscape
The global bio decontamination market, valued at $171.4 million in 2022, is projected to reach $294.7 million by 2030, reflecting a 7% compound annual growth rate. This growth is driven by expanding pharmaceutical and biotechnology sectors, increasing regulatory requirements, and growing awareness of environmental protection needs.
Solution Category | Primary Advantages | Typical Applications | Investment Range |
---|---|---|---|
Thermal Systems | Validated efficacy, broad spectrum | BSL-3/4 facilities, pharmaceutical | $150K-$2M |
Chemical Treatment | Lower capital cost, ambient operation | Research labs, pilot facilities | $50K-$500K |
Membrane Systems | High-quality effluent, resource recovery | Manufacturing, water reuse | $100K-$1.5M |
Integrated Solutions | Comprehensive treatment, regulatory compliance | All facility types | $200K-$5M |
Competitive differentiation in the effluent decontamination market focuses on several key factors: validation support, energy efficiency, operational reliability, and regulatory compliance assistance. Leading systems incorporate advanced control technologies, predictive maintenance capabilities, and modular designs that accommodate facility growth and changing requirements.
Technology trends indicate increasing adoption of digitalization and automation in treatment systems. Cloud-based monitoring platforms enable real-time performance optimization and predictive maintenance, reducing operational disruptions and ensuring consistent compliance. Integration of artificial intelligence and machine learning algorithms promises further improvements in system efficiency and reliability.
The selection criteria for industrial effluent treatment solutions should consider long-term operational costs, scalability, regulatory compliance support, and vendor technical expertise. Facilities benefit from partnerships with experienced providers who understand both the technical requirements and regulatory landscape specific to pharmaceutical and biotechnology applications.
Modern effluent decontamination systems represent essential infrastructure for pharmaceutical and biotechnology facilities operating under increasingly stringent environmental regulations. The combination of thermal, chemical, and membrane treatment technologies provides validated performance across diverse waste streams while supporting operational efficiency and regulatory compliance. As the industry continues evolving toward more sustainable practices, these systems enable facilities to meet current requirements while preparing for future regulatory developments.
Related Contents:
- Safeguarding Health: Advanced Effluent Decontamination Systems
- Sterile Effluent Cooling: BioSafe’s EDS Technology
- BioSafe EDS: Thermal Systems for Effluent Treatment
- BSL-4 Waste Sterilization: Ensuring Safe Disposal
- Navigating Regulatory Waters: Effluent Treatment in Biopharma
- Effluent Segregation: Optimizing EDS Implementation
- BioSafe EDS: Batch-Continuous Treatment Systems
- Waste Effluent Stream Management: BioSafe EDS
- Continuous Effluent Decontamination: Protecting Our Environment